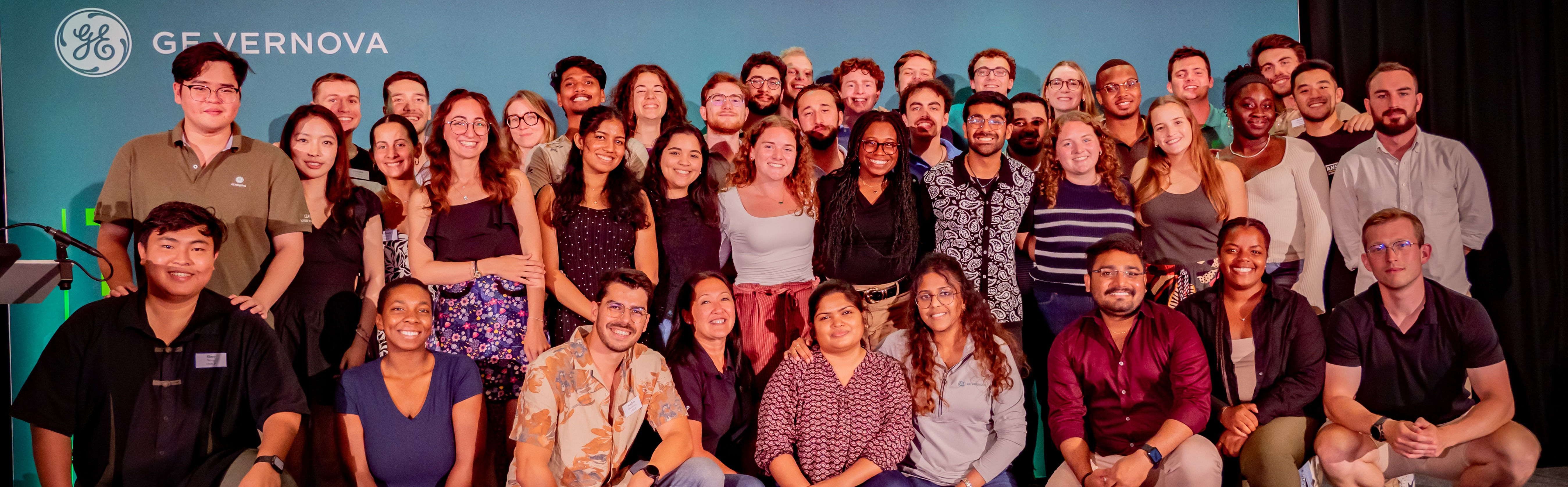
Find your dream job at Phenom People
Lorem Ipsum
OPERATIONS MANAGEMENT DEVELOPMENT PROGRAM
The Operations Management Development Program (OMDP) is a two-year rotational program consisting of four six-month rotations that allow members to build leadership and functional skills through challenging assignments and world-class training. Training topics include lean, functional expertise (EHS, quality, materials, etc.), as well as leadership and personal development topics.
OMDP accelerates development of entry-level talent and produces leaders capable of meeting the challenges facing the Supply Chain (inclusive of manufacturing, sourcing, materials, and quality) functions at GE Vernova. For those that have a passion for technology in the energy sector and want a career in manufacturing/supply chain amidst a lean culture, OMDP is for you!
OMDP accelerates development of entry-level talent and produces leaders capable of meeting the challenges facing the Supply Chain (inclusive of manufacturing, sourcing, materials, and quality) functions at GE Vernova. For those that have a passion for technology in the energy sector and want a career in manufacturing/supply chain amidst a lean culture, OMDP is for you!

lorem ipsum
Mindfulness
Mindfulness, egolessness, and pragmatic craftsmanship are core to our culture—from daily to monthly basis
A sense of mutual respect and mindfulness permeates our culture-in fact, it’s the key to our success.
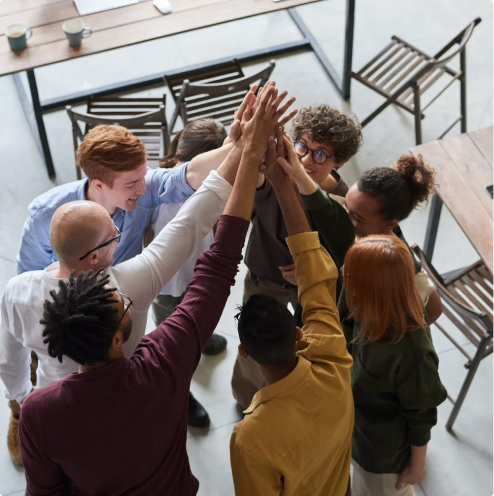
lorem ipsum
Your Family Life
- Two years of on-program experience comprised of performing meaningful customer-focused work
- Four 6-month rotations resulting in real roles, impact, and responsibility
- World-class education opportunities:
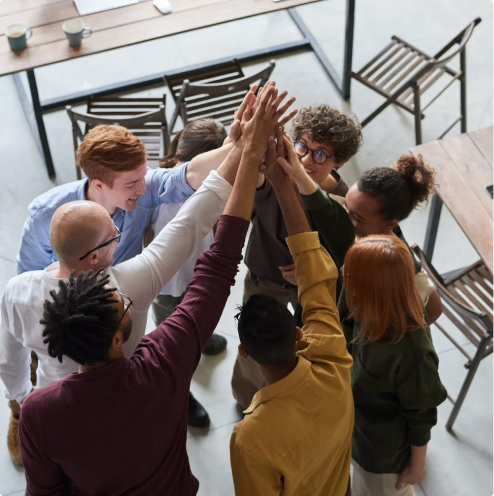
lorem ipsum
Your Family Life
- Industry, Product & Leadership Training
- Functional Development in EHS, Quality, and Materials
- Lean Development and APICS CPIM certification
- Train, work and learn with a globally diverse community of young professionals
A sense of mutual respect and mindfulness permeates our culture-in fact, it’s the key to our success.
Developing our next generation
of leaders & innovators
A sense of mutual respect and mindfulness permeates our culture-in fact, it’s the key to our success.
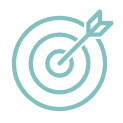
lorem ipsum
IMPACT
At GE Vernova, we work to solve one of the world’s biggest challenges – to meet the rising global demand for affordable, reliable, and sustainable energy and lead the industries' decarbonization efforts to address climate change.
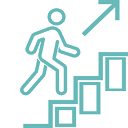
lorem ipsum
INVESTMENT
Participants will experience world-class training, including functional course work, continuous coaching, exposure to executive leadership, and global experiences.
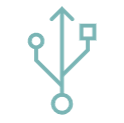
lorem ipsum
OUTCOMES
Our program provides accelerated learning and professional development through rotational experiences, with the goal of generating our future leaders.
A sense of mutual respect and mindfulness permeates our culture-in fact, it’s the key to our success.
Why work here?
A sense of mutual respect and mindfulness permeates our culture-in fact, it’s the key to our success.

lorem ipsum
Mindfulness
Mindfulness, egolessness, and pragmatic craftsmanship are core to our culture—from daily to monthly basis
A sense of mutual respect and mindfulness permeates our culture-in fact, it’s the key to our success.
Lorem Ipsum has been the industry's standard dummy text
Lorem Ipsum has been the industry's standard dummy text ever since the 1500s, when an unknown printer took a galley of type and scrambled it to make a type specimen book.
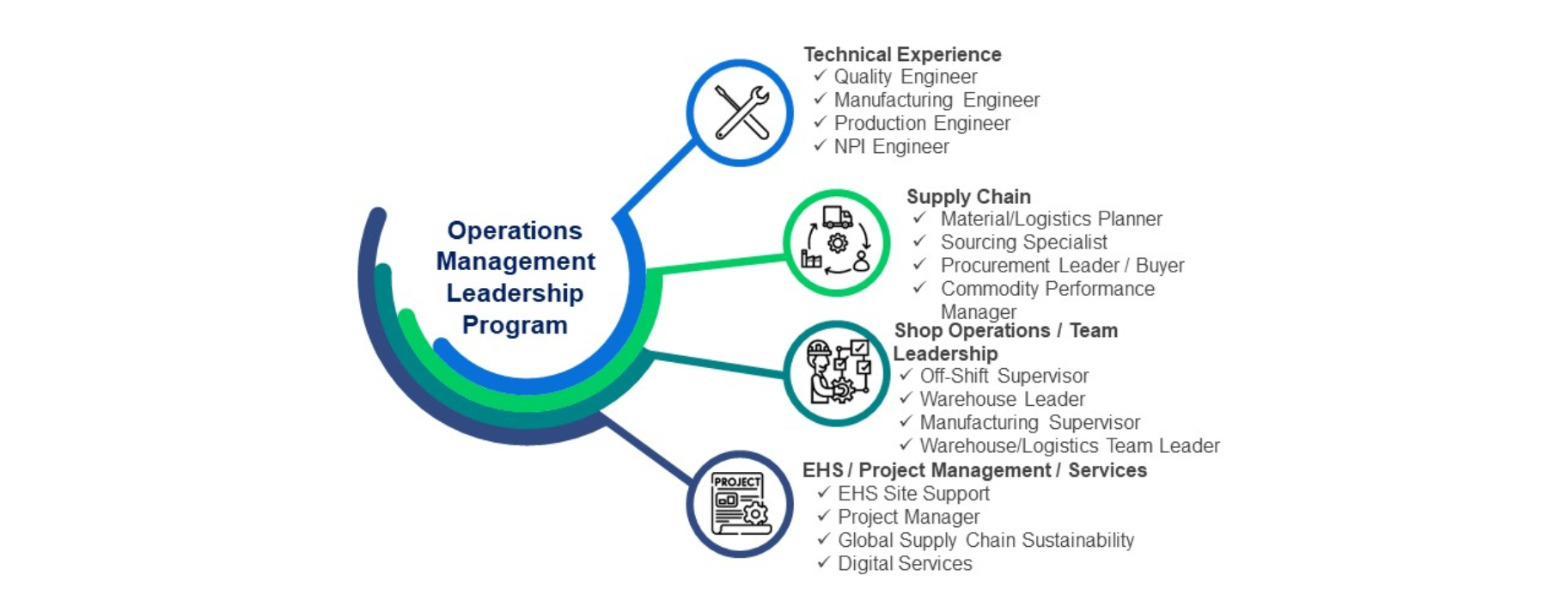
A sense of mutual respect and mindfulness permeates our culture-in fact, it’s the key to our success.
Developing our next generation
of leaders & innovators
A sense of mutual respect and mindfulness permeates our culture-in fact, it’s the key to our success.
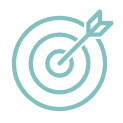
lorem ipsum
Quality Engineer
In this rotation, I worked cross functionally with engineering, sourcing, manufacturing, and operators to determine the most efficient ways to decrease the number of defects in our manufacturing and services process. Daily, I would work with subject matter experts to determine root causes on quality issues created through our current process, we would implement countermeasures to correct and prevent the recurrence of quality issues, and then run statistical analysis to understand the impact and overall improvement. Statistical analysis also helped us drive the problem-solving process for our manufacturing facilities as a whole.
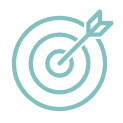
lorem ipsum
Manufacturing Engineer
In this rotation I worked as a project manager within a cross functional team, tasked with multiple projects throughout the rotation. I would shadow a particular process to identify waste and implement standard work to support a single workflow. We would use LEAN tools like creating a lean roadmap and even organize machine installations and projects to align with new methodology. Once we have established the final process, we would update current methods to ensure that the process is up-to-date and documented for the plant. Some of the skills I learned were a mix of product and process knowledge, paired with influencing and lean soft skills.
A sense of mutual respect and mindfulness permeates our culture-in fact, it’s the key to our success.
Hear from a OMLP member
Lorem ipsum dolor sit amet consectetur adipisicing elit. Inventore assumenda asperiores distinctio est perferendis esse animi maiores dolor numquam nihil sint, et quae nobis harum consequuntur! Assumenda facere magnam nostrum?
A sense of mutual respect and mindfulness permeates our culture-in fact, it’s the key to our success.
Rotation examples
A career at Phenom Foods Market is more than the work you do. impact on the community, your personal growth and team members.
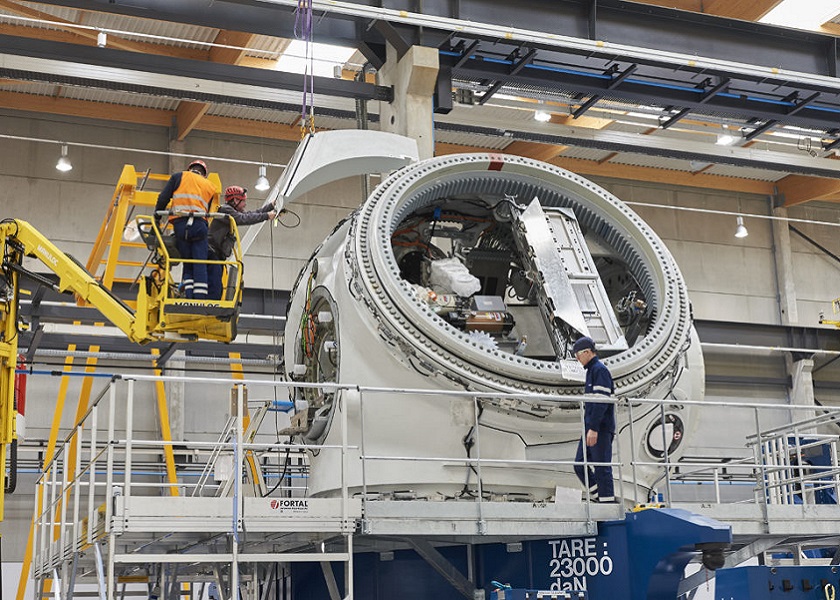
lorem ipsum
Lean Engineer, Pull Implementation – Micromixers
Gavin Calarco
In my third rotation, I supported the Combustion and Repair Materials team in Greenville, SC as a Materials Lean Project Manager. In this role I completed my Capstone project, focused on implementing a materials management strategy referred to as “pull” to our Additive Manufacturing process. Pull helps create a standard set of running rules (what to run, when to run it, and in what quantity), as well as defines Standard Work in Process, or SWIP, levels within a system. This in turn reduces lead time, lead time variability, cost, and the need to expedite/prioritize orders. I led two kaizen events, in which I worked with different manufacturing cells to create lineside kanbans that improved SQDC (Safety, Quality, Delivery, and Cost) for the operations teams. I also completed multiple visual management projects that helped the team understand if the system was operating at normal or abnormal conditions, at a glance.
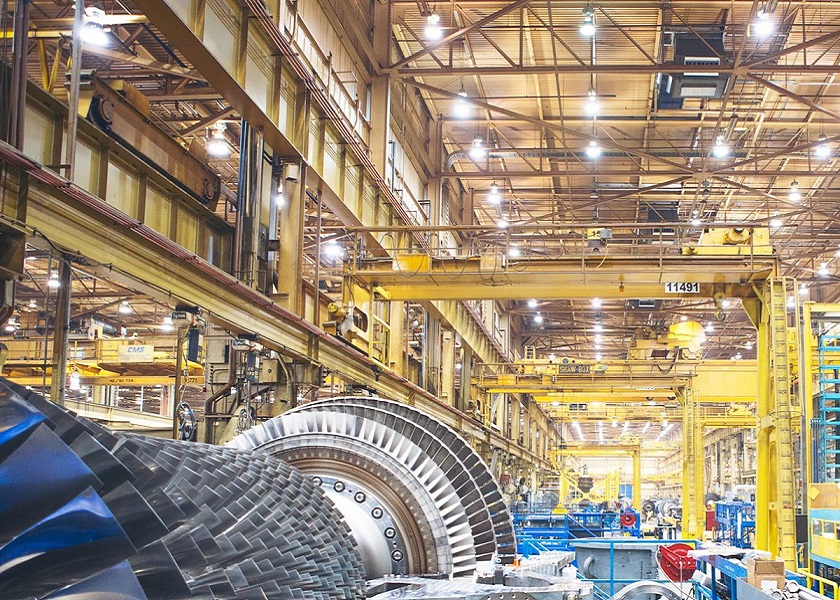
lorem ipsum
Materials Team, Inventory Leader
Luc Booz
During my second OMLP rotation, I was an Inventory Leader for Hot Gas Path in Greenville, South Carolina. The scope of my assignment was largely focused on driving down inventory costs through defining and rolling out procurement policies, facilitating the exchange of excess materials through different GE sites, and working with Quality to develop rework routes for slow moving inventory. Working with the different quality and materials teams in Greenville and across the globe, we were able to eliminate millions of dollars in excess inventory, making it a very fulfilling 6-month assignment. This rotation showed me the importance of collaboration, leadership at the individual contributor level, and the massive business impact of having robust inventory management standards.
A sense of mutual respect and mindfulness permeates our culture-in fact, it’s the key to our success.